axym
Industrial
- Apr 28, 2003
- 1,043
Here is Figure 8-24 from Y14.5-2009, with an additional position tolerance added:
The additional callout refines the relationship of the feature to Datum A.
Is this a valid application? ;^)
Evan Janeshewski
Axymetrix Quality Engineering Inc.
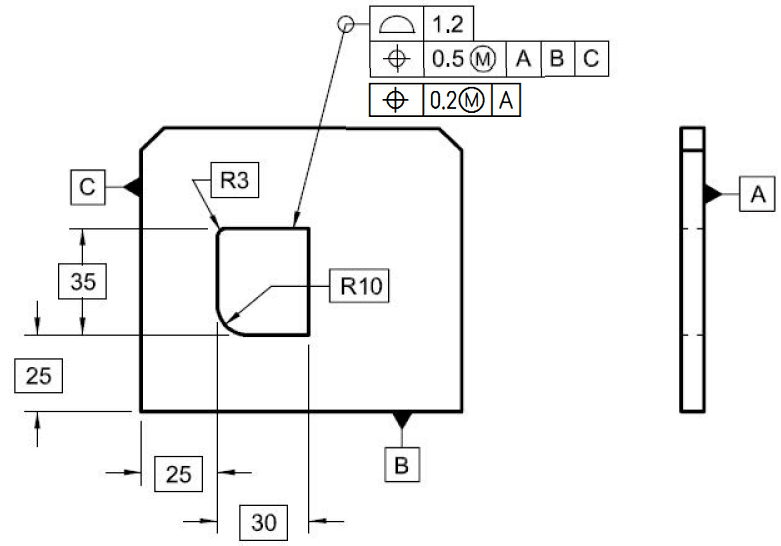
The additional callout refines the relationship of the feature to Datum A.
Is this a valid application? ;^)
Evan Janeshewski
Axymetrix Quality Engineering Inc.