lucky-guesser
Industrial
- Apr 11, 2023
- 137
We have machined stainless parts forever but historically our primary material was brass. People above me have decided that we are switching to 316L as our primary material. Over the past few years, issues with the machineability of the 316L have become more frequent and now that it is our go to material, it is a weekly/daily issue. So not a new issue by any means, just getting to be a bigger one. Parts are rough cast by our supplier and we final machine. We will get a batch of parts that machine well, then the next batch will be riddled with parts that are harder and noticeably more difficult to machine.
Standard practice is 95deg carbide inserts (CNMG 12 04 12-MR 2025) with -5deg lead, full coolant, .050 DOC per side. Our ID cuts are standard boring operations, but OD turning is compounded by being an interrupted cut (more air than metal on the interrupted section). OD is more susceptible to issues when cutting borderline material, but particularly hard parts cause issues on both OD and ID cuts.
The primary issue is chipping of inserts. Problem parts are needing inserts flipped/replaced every pass in extreme cases. When machining brass, we can typically do several parts per insert, but with a problem 316L part it is more like several inserts per part.
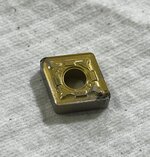
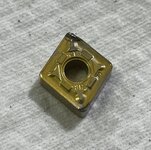
Using our PMI gun, a hard-but-not-awful part tested:
Si: .51%
Cr: 18.92%
Mn: .88%
Fe: 66.68%
Ni: 10.09%
Cu: .32%
Mo: 2.1%
The remaining .5% (including Carbon) in unknown.
Talking to a couple of our most experienced machinists, we have tried:
Numerous different inserts
DOC variations from .020-.200
Various RPM and feed rates (exact range is unknown, but you get the point)
Turning coolant off (OD interrupted cuts)
Annealing in our large oven. Some parts improved but others didn't.
I have instructed the machinists that when they get a particularly hard part again, to let me know and I will do a composition test to compare to the others as well as hopefully a hardness test. Our tester is of the "Telebrineller System" type which is a new one for me so we'll see if I get any meaningful results from that.
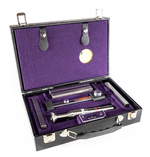
Any insight, experience, suggestions or off the wall conspiracy theories will all be considered helpful at this point. As I read and find another idea, I take it to the machinists and it's something they have already tried. Open to anything at this point, thanks.
Standard practice is 95deg carbide inserts (CNMG 12 04 12-MR 2025) with -5deg lead, full coolant, .050 DOC per side. Our ID cuts are standard boring operations, but OD turning is compounded by being an interrupted cut (more air than metal on the interrupted section). OD is more susceptible to issues when cutting borderline material, but particularly hard parts cause issues on both OD and ID cuts.
The primary issue is chipping of inserts. Problem parts are needing inserts flipped/replaced every pass in extreme cases. When machining brass, we can typically do several parts per insert, but with a problem 316L part it is more like several inserts per part.
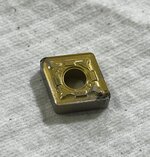
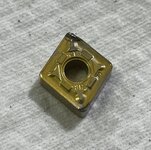
Using our PMI gun, a hard-but-not-awful part tested:
Si: .51%
Cr: 18.92%
Mn: .88%
Fe: 66.68%
Ni: 10.09%
Cu: .32%
Mo: 2.1%
The remaining .5% (including Carbon) in unknown.
Talking to a couple of our most experienced machinists, we have tried:
Numerous different inserts
DOC variations from .020-.200
Various RPM and feed rates (exact range is unknown, but you get the point)
Turning coolant off (OD interrupted cuts)
Annealing in our large oven. Some parts improved but others didn't.
I have instructed the machinists that when they get a particularly hard part again, to let me know and I will do a composition test to compare to the others as well as hopefully a hardness test. Our tester is of the "Telebrineller System" type which is a new one for me so we'll see if I get any meaningful results from that.
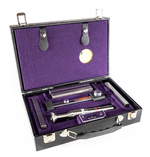
Any insight, experience, suggestions or off the wall conspiracy theories will all be considered helpful at this point. As I read and find another idea, I take it to the machinists and it's something they have already tried. Open to anything at this point, thanks.