willtech
Automotive
- Feb 23, 2011
- 4
Hi ENG tips.
I am designing a large rolling rig which is essentially used to house and turn a film set. In essence it is a base frame with a motor connected to a drive wheel which in turn is acting on a large 10 meter diameter ring. It is within this circular ring that a set would be built.
I am in early stages of design and would like to spec a motor early to help with the drawing process. I have simplified the rig onto one plane (see drawing)in the hope someone can feedback with a suitable calc for motor torque and power post gearbox?
Here are a few details regarding the rig-
10 meter diameter ring 720kg.
rubber drive wheel 500mm diameter.
needs to rotate at 10rpm max.
maximun 5000kg internal load of set, performers etc... this should be evenly distributed but with performers and crew running around this could change a little so redundancy might be wise.
Please see attached images, one of existing rig to give you the idea and one very early drawing of the rig i am designing.
Any help greatly appreciated!!!
I am designing a large rolling rig which is essentially used to house and turn a film set. In essence it is a base frame with a motor connected to a drive wheel which in turn is acting on a large 10 meter diameter ring. It is within this circular ring that a set would be built.
I am in early stages of design and would like to spec a motor early to help with the drawing process. I have simplified the rig onto one plane (see drawing)in the hope someone can feedback with a suitable calc for motor torque and power post gearbox?
Here are a few details regarding the rig-
10 meter diameter ring 720kg.
rubber drive wheel 500mm diameter.
needs to rotate at 10rpm max.
maximun 5000kg internal load of set, performers etc... this should be evenly distributed but with performers and crew running around this could change a little so redundancy might be wise.
Please see attached images, one of existing rig to give you the idea and one very early drawing of the rig i am designing.
Any help greatly appreciated!!!
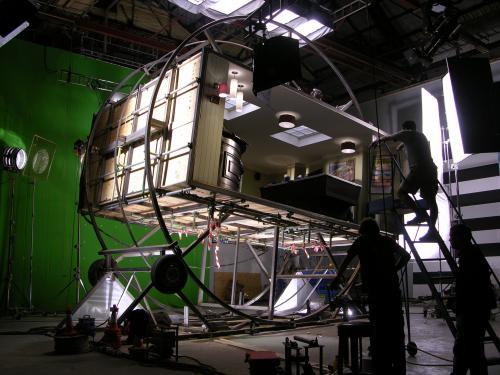
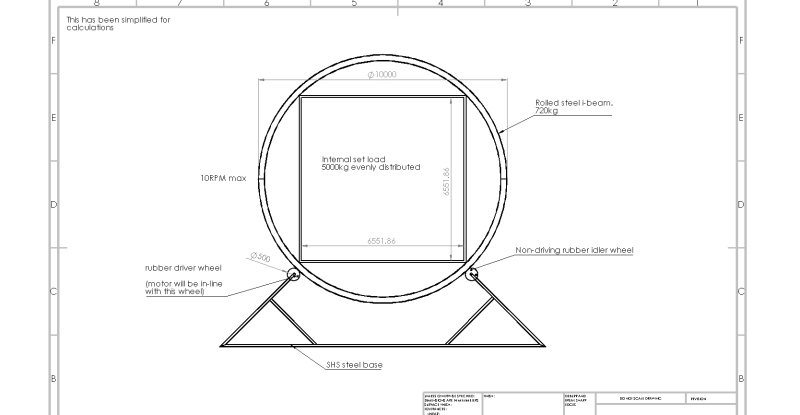