JacobP12345
Mechanical
- Aug 7, 2019
- 20
Thank you in advance to any tips and advice.
My company is currently working on getting production up and running with a Capital Robotics Fusion Arc 180. Our current objective is to perform a consistent outside weld on a piece of stitch cut 14 ga sheet metal folded into a piece of angle. These parts are intended to be mass produced and this type of weld will be replicated on many of our future products. The weld is defective and has many blowholes and splatter throughout it after initial success earlier in the weld. Attached are the images of both a successful weld we are trying to imitate performed by our machine and one of their engineer representatives. The other images are obvious and very typical failures we're experiencing during testing.
Any help is greatly appreciated.
My company is currently working on getting production up and running with a Capital Robotics Fusion Arc 180. Our current objective is to perform a consistent outside weld on a piece of stitch cut 14 ga sheet metal folded into a piece of angle. These parts are intended to be mass produced and this type of weld will be replicated on many of our future products. The weld is defective and has many blowholes and splatter throughout it after initial success earlier in the weld. Attached are the images of both a successful weld we are trying to imitate performed by our machine and one of their engineer representatives. The other images are obvious and very typical failures we're experiencing during testing.
Any help is greatly appreciated.
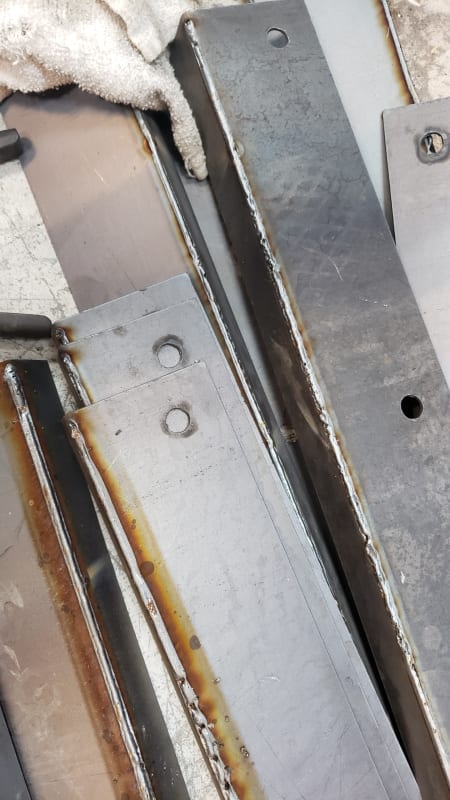
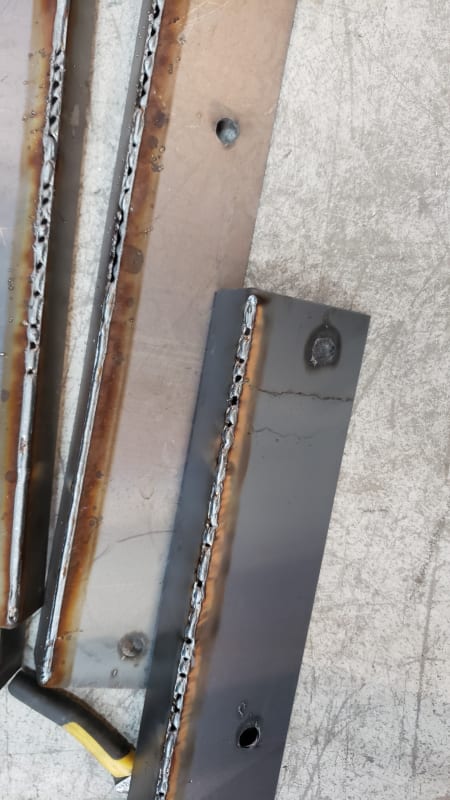
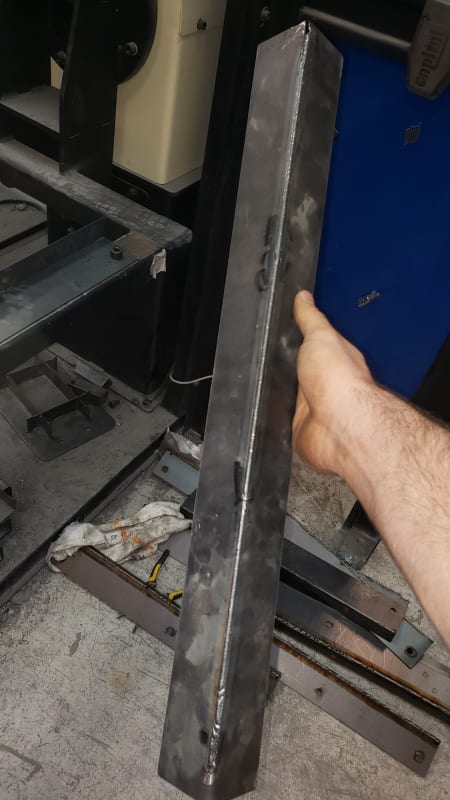