Lawry1183
Petroleum
- Feb 21, 2018
- 5
We have a 20" fuel gas pipeline designed as per ASME B31.8 with permanent pig traps. We have the PID which is indicated below. I would like to get technical insight on the requirement of this valve.
Second query on same PID - Also as per Design engineering practice for pipelines, " use of fittings between isolation valves, such as flanges and instrument taps shall be avoided". Does this means SDV shall be welded type rather than flanged?
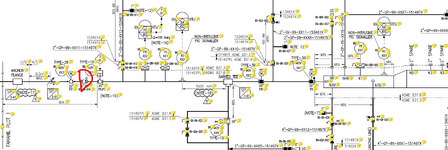
Second query on same PID - Also as per Design engineering practice for pipelines, " use of fittings between isolation valves, such as flanges and instrument taps shall be avoided". Does this means SDV shall be welded type rather than flanged?
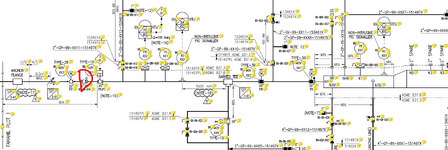