sirbrandon
Mechanical
- Jan 4, 2009
- 19
Hi,
I read about the dangers of double dependency when using RBE2. I have a problem (see attached pic) where I need to mount two components one the same platform, one component on the top surface, the other on the bottom surface. I tried running the sample problem with AUTOMPC ON, and it seems to run ok. Can anyone advise if this approach is ok? How else would you model the problem if I were to avoid having double dependency in this case? Thanks.
I read about the dangers of double dependency when using RBE2. I have a problem (see attached pic) where I need to mount two components one the same platform, one component on the top surface, the other on the bottom surface. I tried running the sample problem with AUTOMPC ON, and it seems to run ok. Can anyone advise if this approach is ok? How else would you model the problem if I were to avoid having double dependency in this case? Thanks.
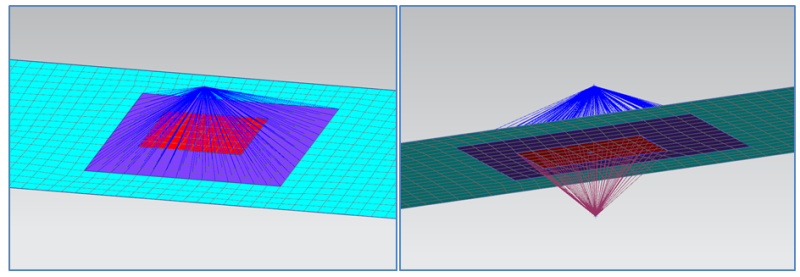