Imposter666
Mechanical
- Jan 15, 2021
- 36
There is a maintenance inspection at this pin once a month. it is usually changed out right away as failure would be catastrophic for the production. I have summarized all the details in the picture below. Increasing pin diameter would definitely help as the contact area would increase. However, I don't think this would solve the problem completely on its own. I didn't want to make radical changes to the design. But I am willing to if it will get rid of the problem completely. What countermeasures do you think can be done here.
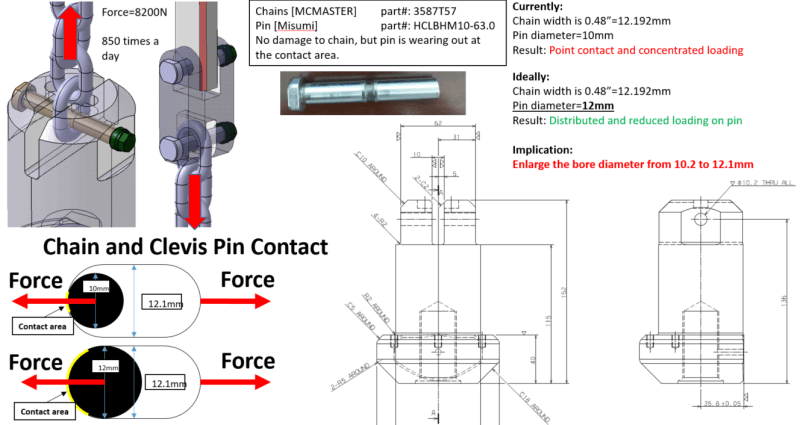