SeasonLee
Mechanical
- Sep 15, 2008
- 918
Hi All
Please ref to Fig. 12-2 of Y14.5-2018 as shown below
I have a question at "Means this", how can a 0.2 tolerance floating within a 0.03 tolerance zone? Please let me know if anything I missed here. Thanks for your help.
Season
Please ref to Fig. 12-2 of Y14.5-2018 as shown below
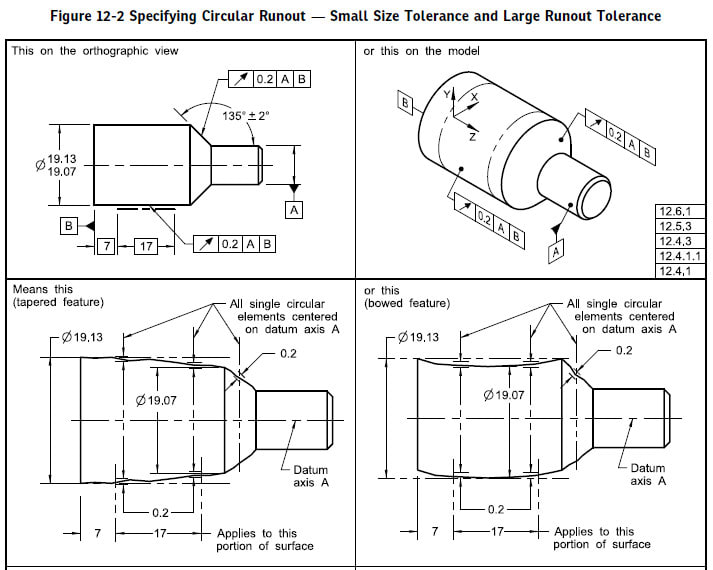
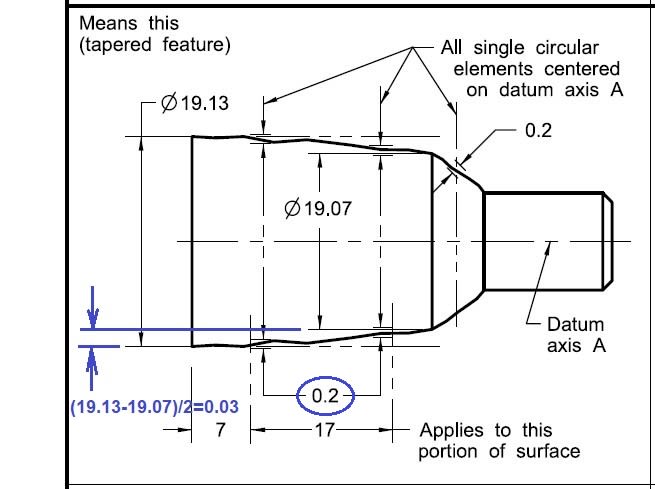
I have a question at "Means this", how can a 0.2 tolerance floating within a 0.03 tolerance zone? Please let me know if anything I missed here. Thanks for your help.
Season