Italo01
Structural
- Sep 4, 2021
- 169
Hello,
I have a question regarding Conrete Breakout strength. The strength of the anchor group to Breakout varies with exponent 3/2 or 5/3, depending on the anchorage length. If the area of the Cone reaches the edges, i.e., AN is maximum, the strength will decrease with a anchorage length increase. Does Anyone know why this happens?
Thank You.
I have a question regarding Conrete Breakout strength. The strength of the anchor group to Breakout varies with exponent 3/2 or 5/3, depending on the anchorage length. If the area of the Cone reaches the edges, i.e., AN is maximum, the strength will decrease with a anchorage length increase. Does Anyone know why this happens?
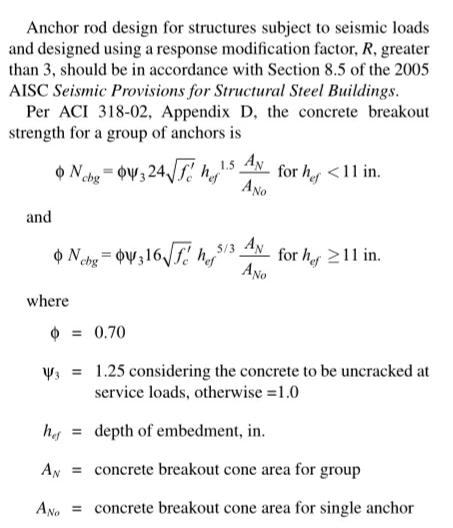
Thank You.