SiggiN
Marine/Ocean
- Mar 18, 2019
- 33
Hi!
Suppose you have two circular segments welded to a pipe as shown below (pad eye plate prevents me to use a full circle)
These segments act as a "tempoary hang-off flange" and will see see a load like this:
I am curious about how to verify the weld size.
Initially I imagined using a force pair, but that will not take the effect of curvature into account?
I am assuming no bending stress in the top weld (only shear)
Would it be (more) correct to use the moment of inertia in the center of the bottom weld to calculate the bending stress in the weld:
sigma_bending = (M/I)*r
("r" being the outer radius of the pipe)
Any thoughts would be appreciated
Thank you!
Regards
Suppose you have two circular segments welded to a pipe as shown below (pad eye plate prevents me to use a full circle)
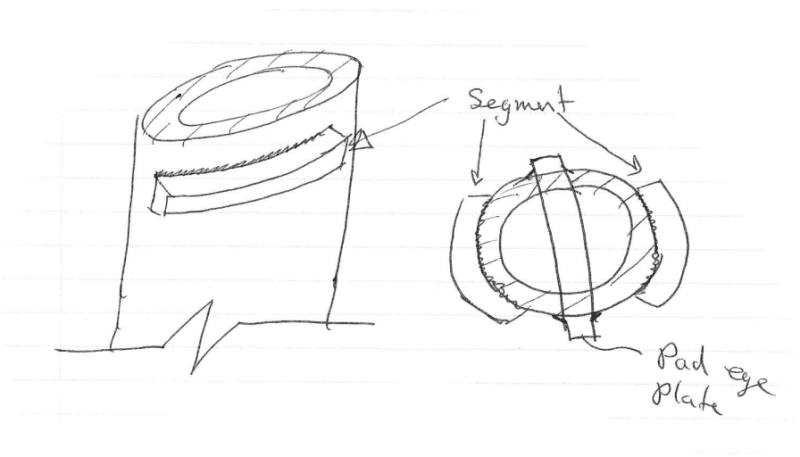
These segments act as a "tempoary hang-off flange" and will see see a load like this:
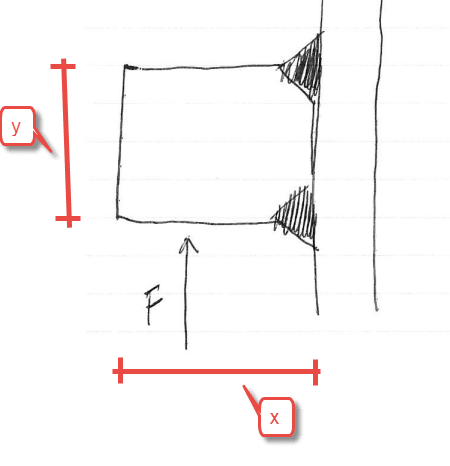
I am curious about how to verify the weld size.
Initially I imagined using a force pair, but that will not take the effect of curvature into account?
I am assuming no bending stress in the top weld (only shear)
Would it be (more) correct to use the moment of inertia in the center of the bottom weld to calculate the bending stress in the weld:
sigma_bending = (M/I)*r
("r" being the outer radius of the pipe)
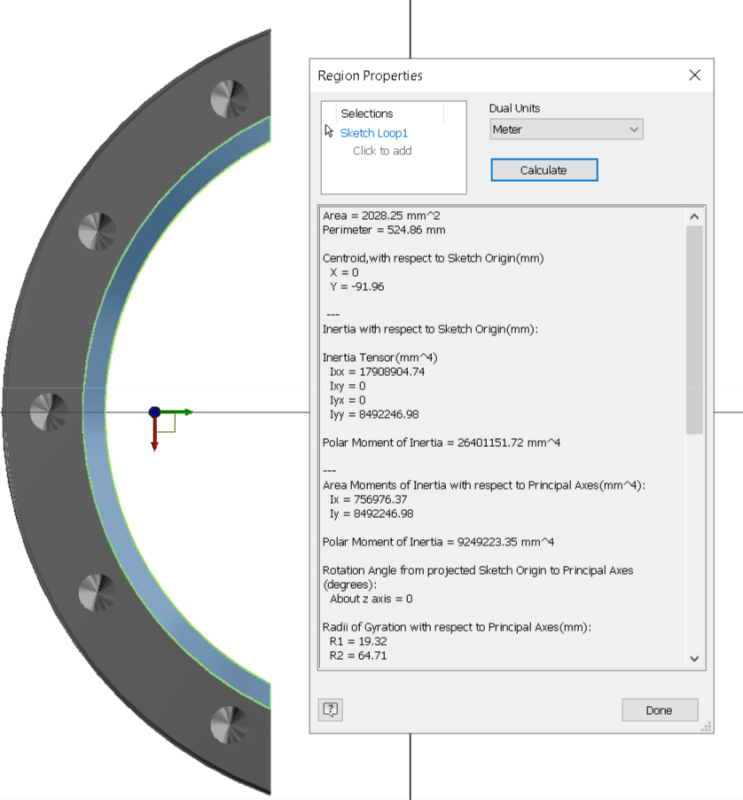
Any thoughts would be appreciated
Thank you!
Regards