Brad805
Structural
- Oct 26, 2010
- 1,518
We are asked from time to time to design slender concrete column elements that are beyond the moment magnification method. We have been testing some random designs using non-linear finite element analysis and correlated one model to an actual test we found. Our prediction was very close to the test data. For our model we used material properties found in the CEB-fip 2010 model code (MC2010), and would like to do so going forward. We are located in Canada and the CSA code is not very verbose on this topic. ACI is better, but does not have the same material property definitions as the model code. I am interested to know if others would be comfortable using the model code if not referenced in their countries code or would you simply say no when asked for this type of design?
CSA code Reference:
ACI
CSA code Reference:
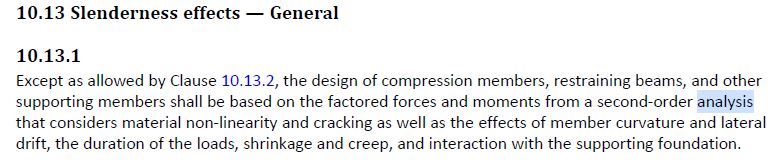
ACI
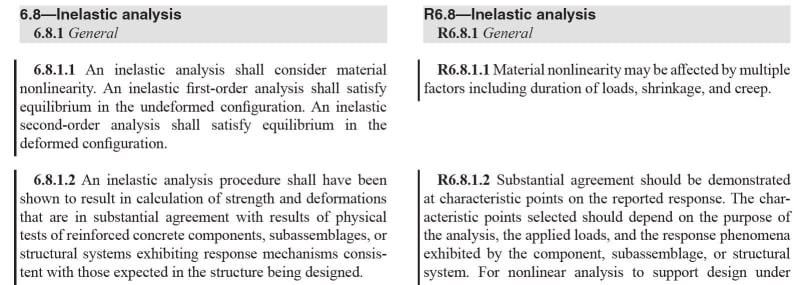