dculp1
Mechanical
- May 16, 2006
- 75
The image shows a plate with a 10mm wide slot. In this design the slot's end shape is a 20mm x 10mm ellipse. A uniform tensile load is applied to the plate's top surface (the narrow surface at the top of the image). Compared to a slot with an R5mm end shape, the von Mises stress is 23% lower.
Besides an ellipse (and possibly a polynomial), what other end shapes should I consider in order to minimize the stress? (I seem to recall a shape that approximated the surface streamline of a fluid flowing through an orifice but I haven't been able to find this again.)
Thanks,
Don C.
Besides an ellipse (and possibly a polynomial), what other end shapes should I consider in order to minimize the stress? (I seem to recall a shape that approximated the surface streamline of a fluid flowing through an orifice but I haven't been able to find this again.)
Thanks,
Don C.
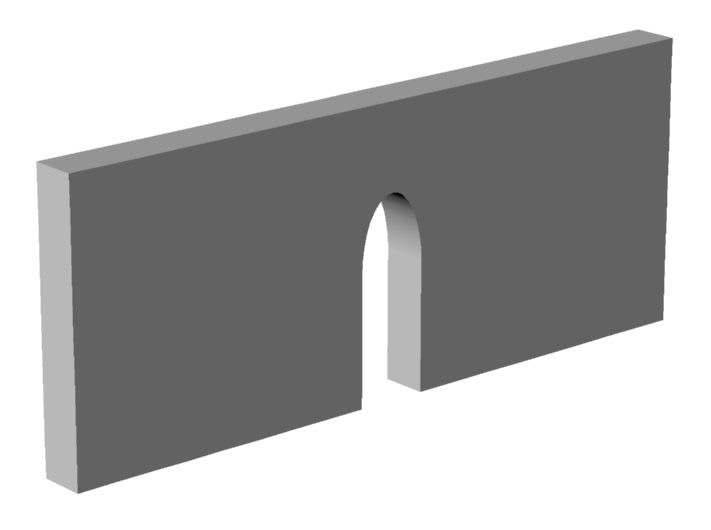