Brad805
Structural
- Oct 26, 2010
- 1,518
I have a project that came back on to my desk, and I have many reservations about what is proposed. I have included a plan view and elevation below. This is to be a climbing wall. It first started with the owners cardboard plan, and after I insisted, they found an EOR that is supposed to have experience in climbing walls. I do not think they looked at the feasibility of what our client suggested to them. Our client has never had a great appreciation for lateral loads or slenderness. I have not gotten far into this, and I would like some general thoughts. It is in a low seismic zone, so the load governing the problem is the 25psf wind load. The EOR has specified some gravity loads at the top of the panel, but those will not be a huge challenge if the general design is stable.
My problems:
1. 6" does not pass the general stink test in my mind.
2. Joints at intersections will need to be dry connections. They will be of paramount importance. I will never win the argument to field cast proper joints that would make my job far easier.
3. Base connections they will want will be simple dowels. Non-contact splices.
4. Only 4 pieces, so eng budget not great.
I can likely persuade them to go to an 8" wall, and add flanges to the ends of the wing panels. My question is do you think it is feasible or possible?
My problems:
1. 6" does not pass the general stink test in my mind.
2. Joints at intersections will need to be dry connections. They will be of paramount importance. I will never win the argument to field cast proper joints that would make my job far easier.
3. Base connections they will want will be simple dowels. Non-contact splices.
4. Only 4 pieces, so eng budget not great.
I can likely persuade them to go to an 8" wall, and add flanges to the ends of the wing panels. My question is do you think it is feasible or possible?
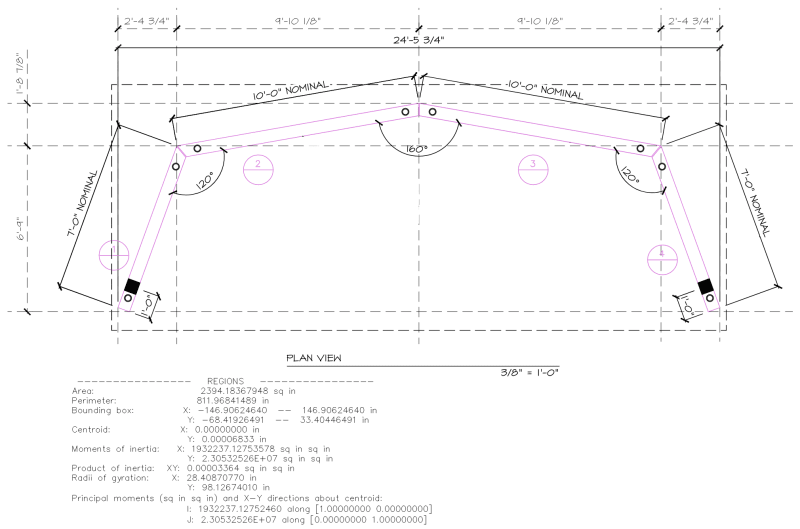
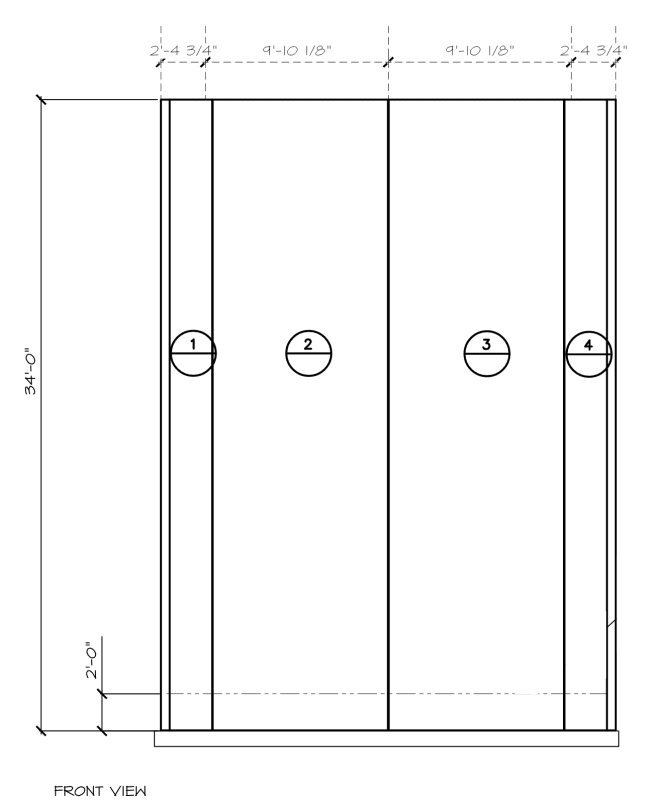