Papachabre
Mechanical
- Jun 30, 2011
- 6
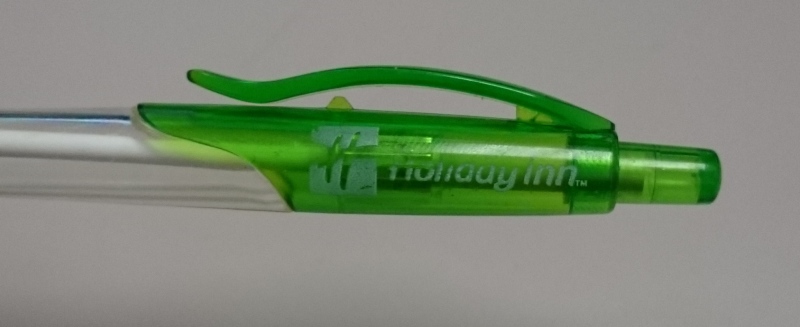
Does anyone know how this pen pocket clip could have been formed? It's all one piece, so either there was some seriously thin steel that formed it, or there's a secondary operation which seems pricey for a throwaway pen. It's parted parallel to the view.
Regards,
Bryan