BlckHwk
Student
- Jul 6, 2023
- 3
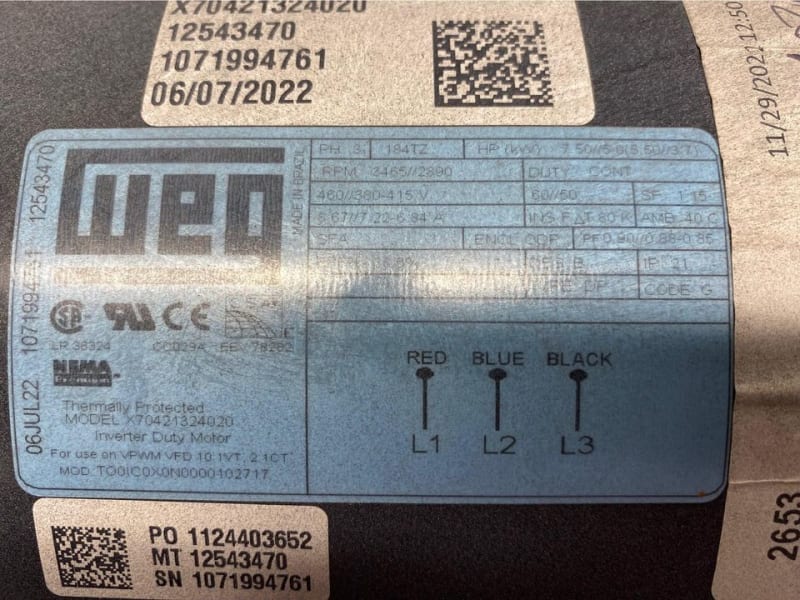
I would like to run this motor using 240 Volt single phase. I am thinking that I would require a VFD to go from single phase to three phase power but not sure about the voltage difference. The motor is going to be used to turn a tumbler which will have very low rotational RPM, between 15 and 25 would be optional, but it will be heavy so the motor will be required to supply a substantial torque load. The tumbler will be 8 foot in diameter, and hold 50 - 100 lbs of medium along with game furs. Total weight inside the tumbler is planned to be around 200 pounds. The tumbler itself is probably around 100/150 pounds, it has pillow block bearings on with axles on each side. It uses a drive sprocket and chain to turn the axle. I already plan on using gear reduction to slow the rotational speed, most likely adjusted with the VFD. My questions are, will this motor run using 240 volt 100 amp current? It does not need to turn at optional power or speed. If not is there a way to raise the home 240 volts to 480 volts which isn't overly pricey (approximately $500 or less)? What size or type VFD would I need? Any other information I should know?
Thanks,
Robin