bmw318be
Mechanical
- Jun 16, 2010
- 197
Hi Just wonder, understand that a centrifugal is not a constant flow device, have Some doubts on the parameter to considered in the frictional loss calculation.
Let say we have following system for simplicity
1. Horizontal line 200 Feet (Pipe 2 to 7 As illustration)
2. Elevation 0 m
3. Elbow 0
4. Tee 2
5. Pipe & Fitting size 2 Inch
6. Centrifugal Pump 200 GPM Head 140 Feet
Q1. In calculating pressure loss, what flow rate to be considered ?.
If we use maximum flow of 200 GPM, it may not be the case as when the pipe emptied, the flow would be 200 GPM and when it gradually filled the pipe, the friction loss would be accumulated and flow is reduced in respect to time.
Q2. Using Epanet 2.2, the software is able to do modelling a flow system, we would the following Inputs
Can help me understand why there is a need for this node the total frictional losses are determined by the pump performance curve Flow and head.
1. On the Node
2. Flow Base demand
After we model this
1. Centrifugal Pump curve (Flow and Head) 200 GPM 140 Ft head
2. Pipe Size 2" All
3. Pipe Length 100 Feet between Node
4. K value 0.85 Metal pipe
5. Elevation 0
I got weird number when I entered Base demand 0 on all node
Q3.
If modelling using the calculator based on assumption of 150 GPM moving Along 103 Feet Losses for 200 Feet length. In other words, there would still be a flow along the pipe line.
Let say we have following system for simplicity
1. Horizontal line 200 Feet (Pipe 2 to 7 As illustration)
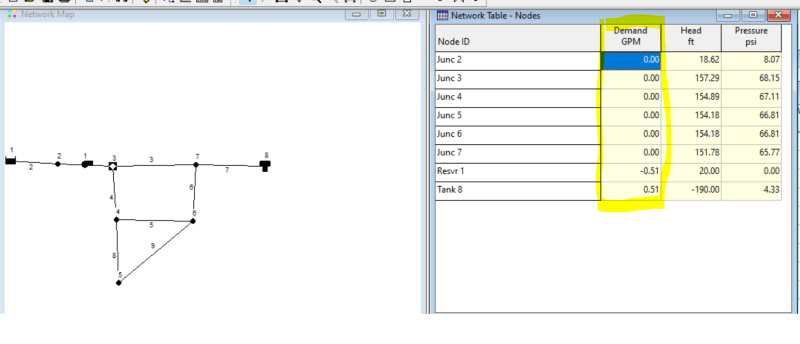
2. Elevation 0 m
3. Elbow 0
4. Tee 2
5. Pipe & Fitting size 2 Inch
6. Centrifugal Pump 200 GPM Head 140 Feet
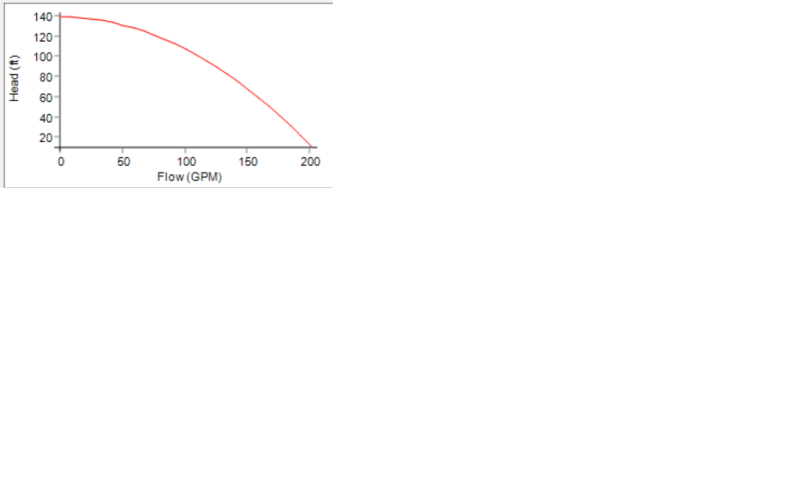
Q1. In calculating pressure loss, what flow rate to be considered ?.
If we use maximum flow of 200 GPM, it may not be the case as when the pipe emptied, the flow would be 200 GPM and when it gradually filled the pipe, the friction loss would be accumulated and flow is reduced in respect to time.
Q2. Using Epanet 2.2, the software is able to do modelling a flow system, we would the following Inputs
Can help me understand why there is a need for this node the total frictional losses are determined by the pump performance curve Flow and head.
1. On the Node
2. Flow Base demand
After we model this
1. Centrifugal Pump curve (Flow and Head) 200 GPM 140 Ft head
2. Pipe Size 2" All
3. Pipe Length 100 Feet between Node
4. K value 0.85 Metal pipe
5. Elevation 0
I got weird number when I entered Base demand 0 on all node
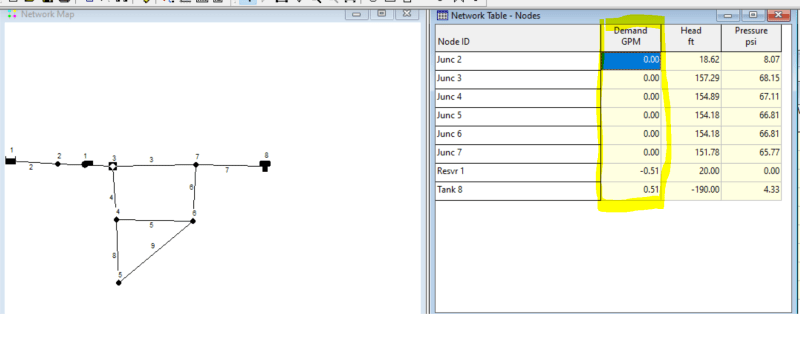
Q3.
If modelling using the calculator based on assumption of 150 GPM moving Along 103 Feet Losses for 200 Feet length. In other words, there would still be a flow along the pipe line.
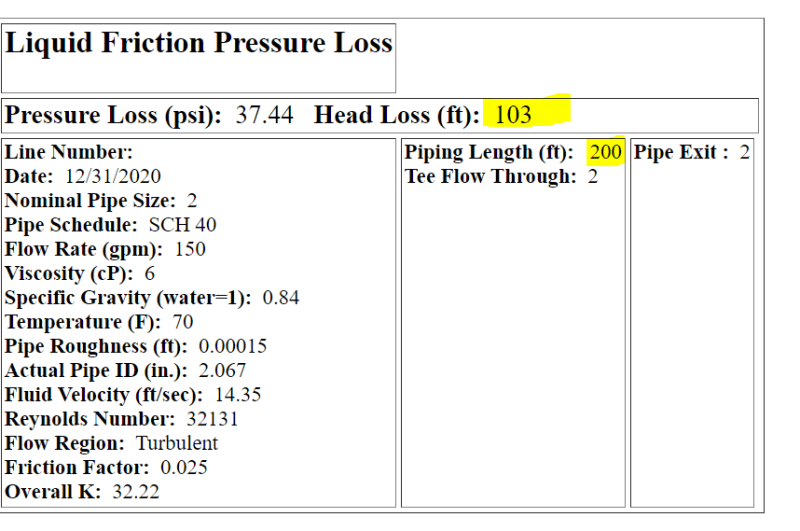