Sajjad2164
Mechanical
- Dec 22, 2015
- 55
Hello, friends!
According to WRC-470, when we have a high temperature in the vessel, there are some methods to reduce the stress level occurring in the skirt-to-head junction including hot-box configuration and using slots to make the region more flexible. I am modeling a vessel on which the designer has put several slots to overcome the high level of thermal stresses. I've encountered a high level of stress concentration. Does anyone have any idea what I should do?
Thanks
According to WRC-470, when we have a high temperature in the vessel, there are some methods to reduce the stress level occurring in the skirt-to-head junction including hot-box configuration and using slots to make the region more flexible. I am modeling a vessel on which the designer has put several slots to overcome the high level of thermal stresses. I've encountered a high level of stress concentration. Does anyone have any idea what I should do?
Thanks
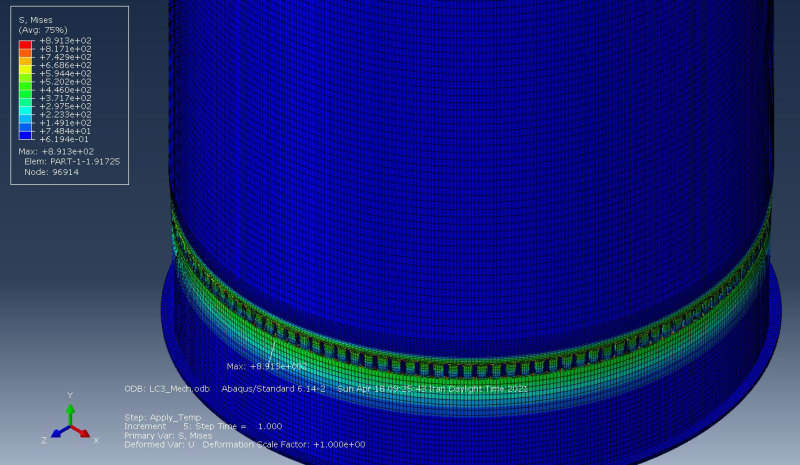