drodrig
Mechanical
- Mar 28, 2013
- 262
Hi,
We have a PE1000 plate with an aluminium plate on the top (900x900mm2 - 35x35inches2). The aluminium plate is cooled by a brass plate-pipe down to -40ºC (-40F). This brass system is in a pocket of the PE1000 plate; there is insulation filling the pocket below the brass.
The aluminium plate is screwed against the PE1000 all around the perimeter. An O-ring seals the perimeter from Isopropanol which is on the top of the aluminium plate.
We chose PE1000 because of its working temperature and the good resistence against the isopropanol, but we overlooked the thermal expansion, which happens to be almost 10 times bigger than the aluminium.
I'm worried this will end up failing. From a quick simulation I get 40MPa when the tensile strength at break is 30MPa.
I would like to ask for some thoughts to solve this. I was thinking about puting an intermediate material (which will keep the PE1000 not so cold) or using Teflon to allow displacements.
thanks
regards,
We have a PE1000 plate with an aluminium plate on the top (900x900mm2 - 35x35inches2). The aluminium plate is cooled by a brass plate-pipe down to -40ºC (-40F). This brass system is in a pocket of the PE1000 plate; there is insulation filling the pocket below the brass.
The aluminium plate is screwed against the PE1000 all around the perimeter. An O-ring seals the perimeter from Isopropanol which is on the top of the aluminium plate.
We chose PE1000 because of its working temperature and the good resistence against the isopropanol, but we overlooked the thermal expansion, which happens to be almost 10 times bigger than the aluminium.
I'm worried this will end up failing. From a quick simulation I get 40MPa when the tensile strength at break is 30MPa.
I would like to ask for some thoughts to solve this. I was thinking about puting an intermediate material (which will keep the PE1000 not so cold) or using Teflon to allow displacements.
thanks
regards,
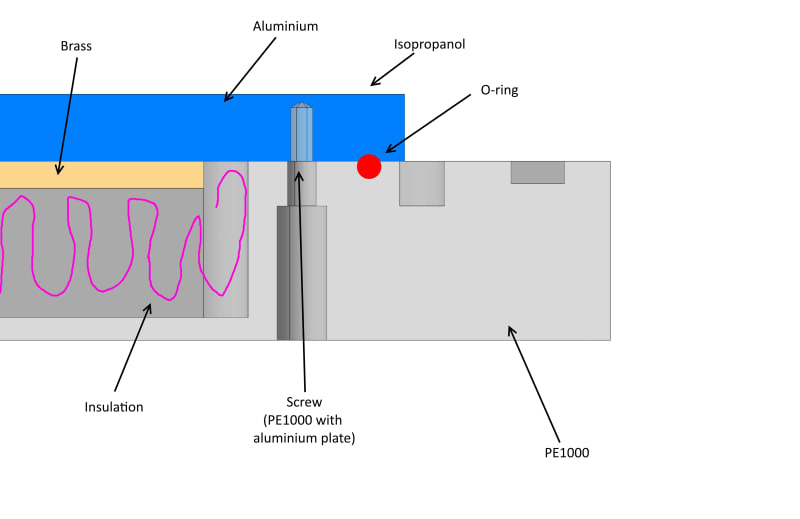
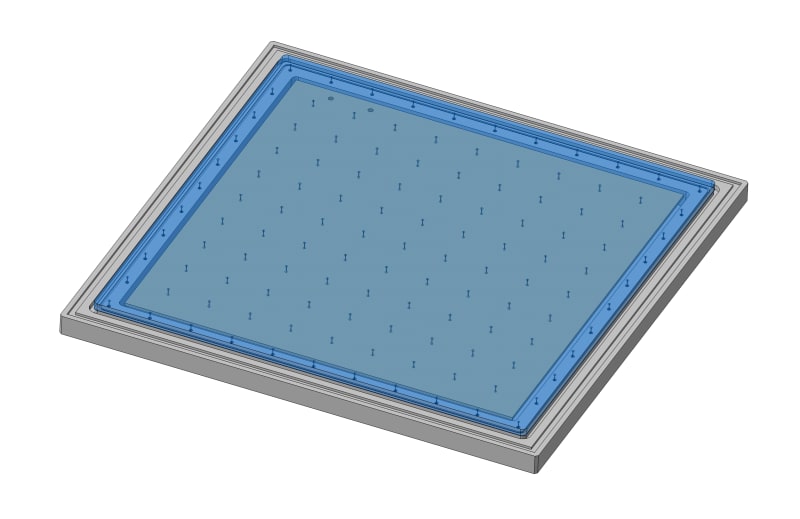