Agent666
Structural
- Jul 2, 2008
- 3,080
After some advice on CLT floor connections between floor panels under diaphragm actions (transferring shear along joints).
I'm finding from a strength perspective we need fixings in joints at very close centres, we can work out the capacity of a screw at minimum spacing, but at some point it seems intuative that the half timber tongue must become a limitation on the capacity that can be transferred in these types of configurations, wondering if anyone has come across any guidance on this.
I've read a lot of advice on CLT joints, but no one seems to recognise this in any design procedures, albeit most of the examples I've seen have relatively wide spacing to the fixings like 200-300mm. Generally it is work out screw capacity, and screw capacity is independent of spacing and potential brittle failures of the connected timber.
But if the fixings are at minimum spacing, say 50-100mm , and you're finding you need multiple rows to achieve the capacity, then does the timber left at the half joint become critical at some point, and if so how to assess?
A few texts mention in passing being aware of splitting when you have close fixings, but that seems to be the grand sum of the advice.
Anyone aware of anything in this space?
I'm finding from a strength perspective we need fixings in joints at very close centres, we can work out the capacity of a screw at minimum spacing, but at some point it seems intuative that the half timber tongue must become a limitation on the capacity that can be transferred in these types of configurations, wondering if anyone has come across any guidance on this.
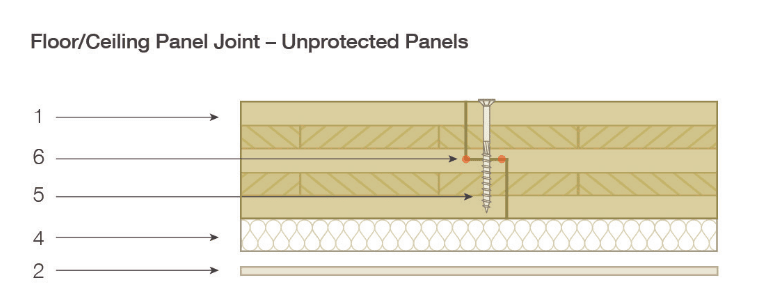
I've read a lot of advice on CLT joints, but no one seems to recognise this in any design procedures, albeit most of the examples I've seen have relatively wide spacing to the fixings like 200-300mm. Generally it is work out screw capacity, and screw capacity is independent of spacing and potential brittle failures of the connected timber.
But if the fixings are at minimum spacing, say 50-100mm , and you're finding you need multiple rows to achieve the capacity, then does the timber left at the half joint become critical at some point, and if so how to assess?
A few texts mention in passing being aware of splitting when you have close fixings, but that seems to be the grand sum of the advice.
Anyone aware of anything in this space?