drodrig
Mechanical
- Mar 28, 2013
- 262
Hi there,
We want to build a cooling shell to get as close as possible to our cooled elements (step shape). It is made of aluminium plates (~20mm thick) bolted together. They will be drilled with two holes each.
There is no much space in the front, so the idea is making a pocket to connect the two holes and then well a cap to close it. On the back we use pipes with a U shape. Here some pictures of the idea:
There is a new proposal to simplify the manufacturing process. Drilling the two holes not through (almost to the end), then perpendicularly from a side make a third hole that connects the two firsts, and then using a cap (which could be even a screw-like cap). I understood this second idea is used in plastic injection moulds.
We use alcohol for cooling (-25ºc/-13ºF).
The second option is easier to build, but I fear the coolant can get in the screw-cap threads gaps and corrode more. If we weld a cap there will be a dead-end.
What do you think?
cheers,
We want to build a cooling shell to get as close as possible to our cooled elements (step shape). It is made of aluminium plates (~20mm thick) bolted together. They will be drilled with two holes each.
There is no much space in the front, so the idea is making a pocket to connect the two holes and then well a cap to close it. On the back we use pipes with a U shape. Here some pictures of the idea:
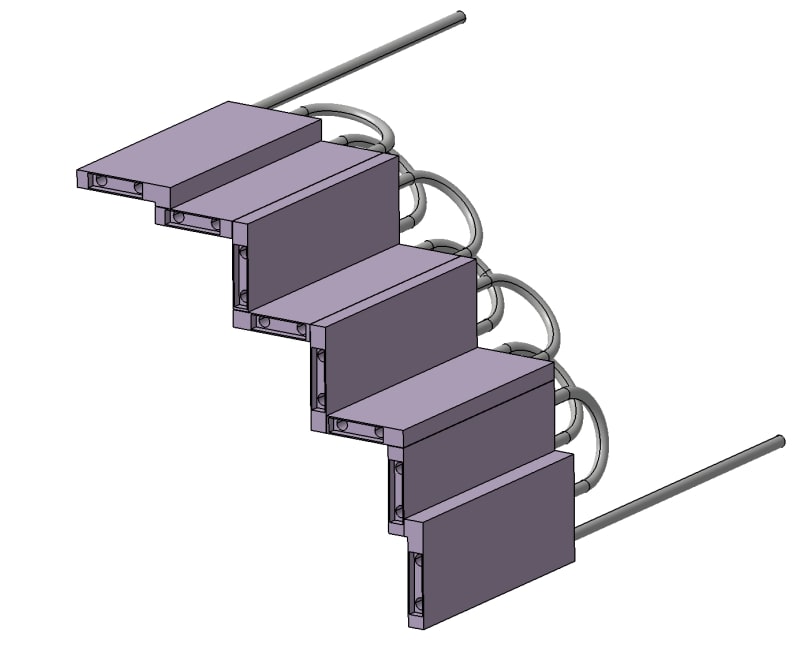
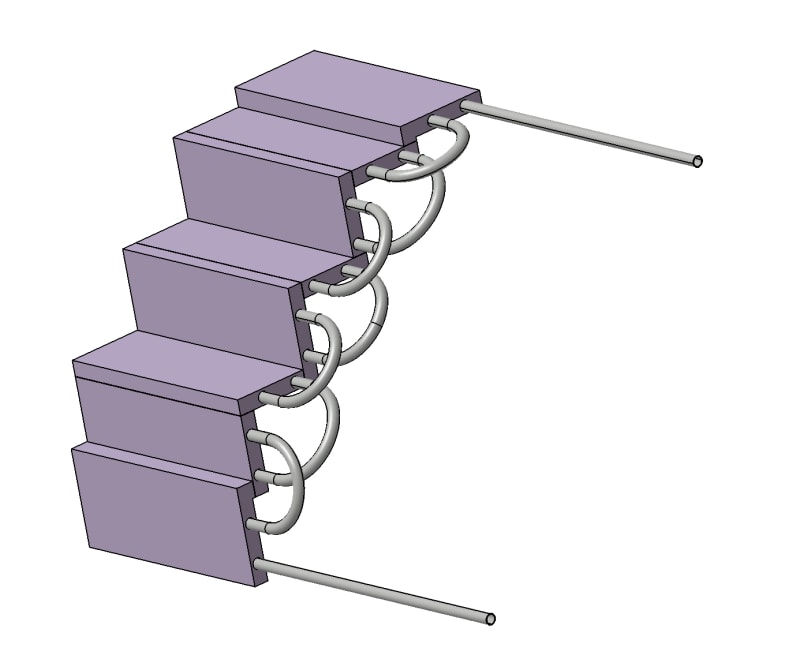
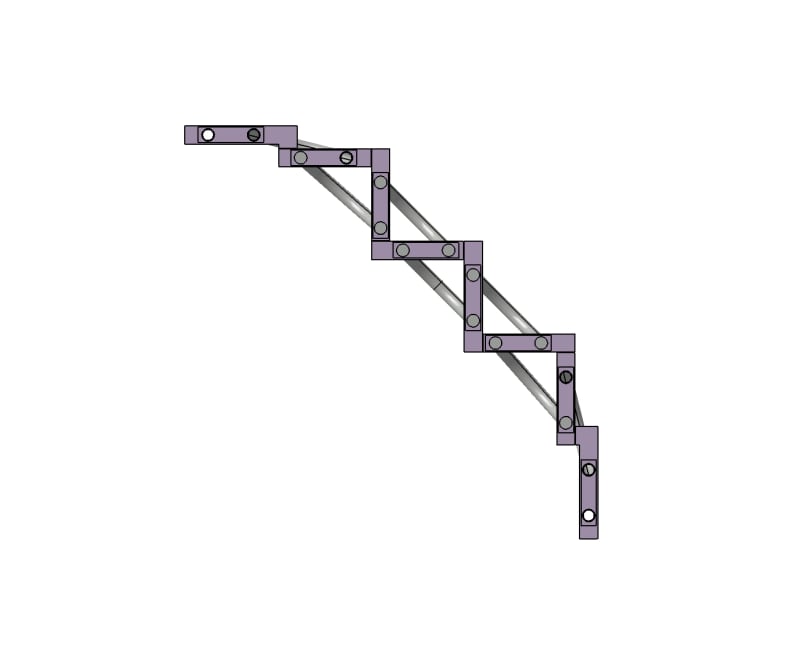
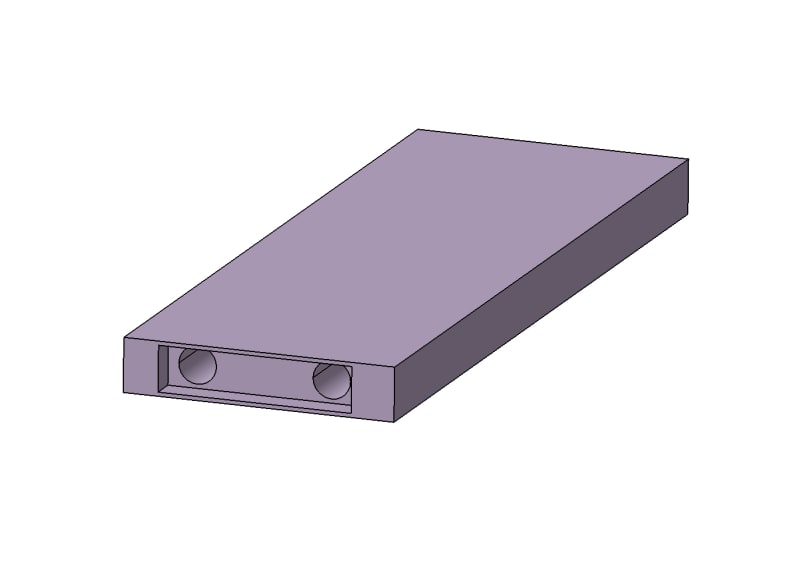
There is a new proposal to simplify the manufacturing process. Drilling the two holes not through (almost to the end), then perpendicularly from a side make a third hole that connects the two firsts, and then using a cap (which could be even a screw-like cap). I understood this second idea is used in plastic injection moulds.
We use alcohol for cooling (-25ºc/-13ºF).
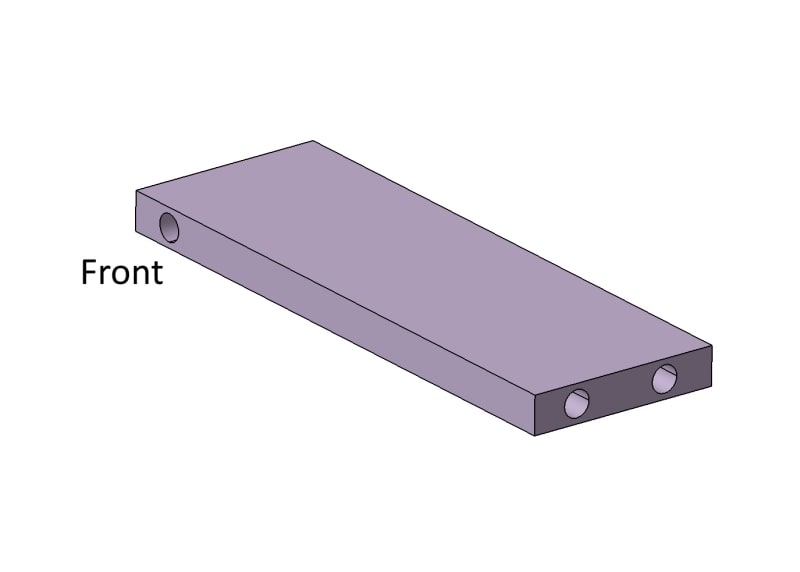
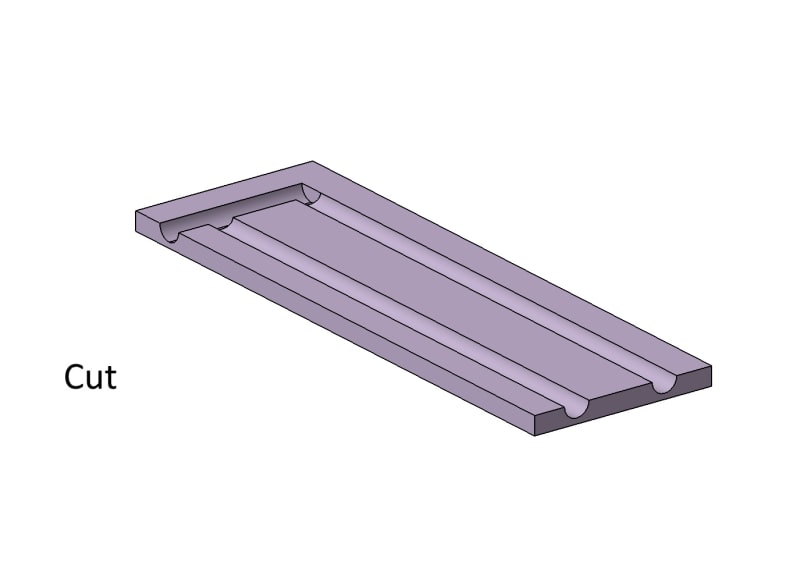
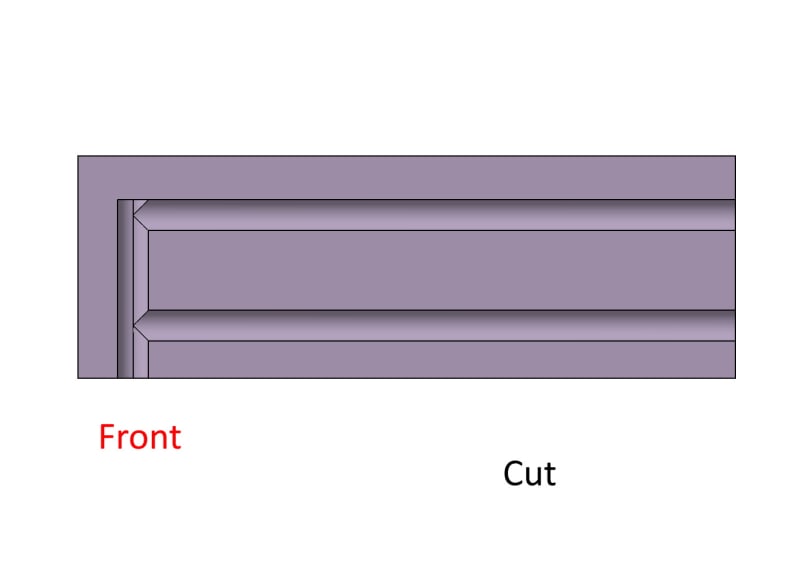
The second option is easier to build, but I fear the coolant can get in the screw-cap threads gaps and corrode more. If we weld a cap there will be a dead-end.
What do you think?
cheers,